[한국형 창조경제 성공으로 가는 길-2부] (11) 현대·기아차 美 생산공장을 가다
섀시 매리지(Chassis marriage)는 자동차 차체(보디)와 엔진, 변속기 등 핵심부품인 섀시가 만나 ‘결혼’을 한다는 뜻이다. 겉모습을 갖춘 프레임에 차를 굴러가게 하는 구동장치가 결합하기 때문에 자동차 제조의 핵심 공정으로 불린다. 지난달 10일 찾아간 미국 조지아주 웨스트포인트시의 기아자동차 공장(KMMG)에서는 4인 1조로 구성된 현지 근로자들이 섀시 매리지 라인에서 일사불란하게 움직이며 3~5분당 한 개꼴로 보디와 섀시를 조립하고 있었다. 기아차 공장과 이곳에서 134㎞ 떨어진 앨라배마주 몽고메리시의 현대자동차 공장(HMMA)은 현대·기아자동차의 미국 생산기지다. 두 공장에서 한 해 생산되는 차는 70만대 이상이다. 만들어진 차는 재고로 쌓일 틈 없이 미국 전역의 판매대리점으로 옮겨가 팔려 나간다. 두 공장이 자동차의 본고장 미국에 진출한 현대·기아차의 심장인 셈이다.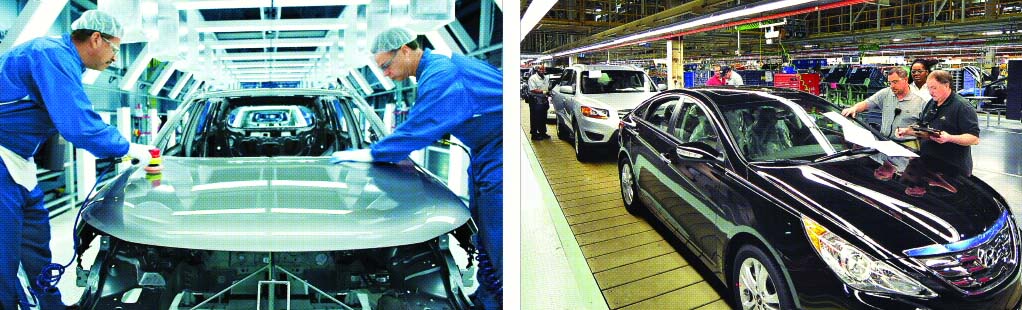
현대·기아자동차 제공
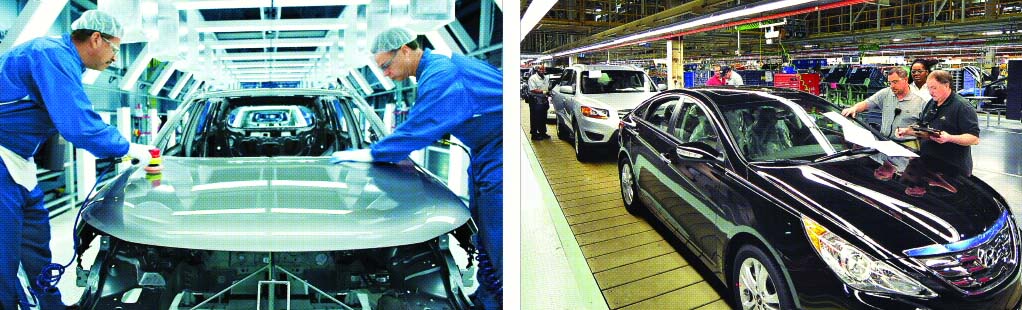
기아자동차 조지아 공장에서 현지 생산 근로자들이 도장되어 나온 차체에 마무리 작업을 하고 있다(왼쪽). 현대자동차 앨라배마 공장에서 품질 관리 직원들이 완성된 차량을 점검하고 있다.
현대·기아자동차 제공
현대·기아자동차 제공
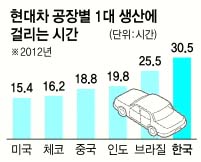
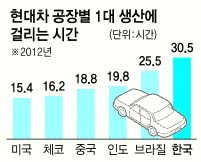
애슐리 프리예 HMMA 생산담당 부사장은 “작업시간에 휴대전화를 사용하면 징계를 받고, 징계가 서너번 누적되면 해고 사유가 된다”면서 “작업장의 도덕규범을 지키는 것이 생산성의 기본”이라고 말했다.
HMMA는 지난해 9월 기존 주야 2교대(10시간씩 근무)에서 24시간 생산체제인 3교대(8시간씩)로 전환했다. 미국 내 판매량에 비해 공급량이 달려 추가로 공장을 돌려야 했기 때문이다. 근무조가 2개에서 3개로 늘어나면서 870명의 신규 인력이 채용됐다. 기존 근로자들은 근로시간이 2시간 줄어든 데 따른 임금 감소를 자연스럽게 받아들였다. 실제 근로자들의 평균 연봉(평일 근무 기준, 특근 제외)은 6만 4275달러에서 4만 8095달러로 25% 줄었다. 김영일 HMMA 부장은 “임금이 줄었지만 대신 가족과 함께할 시간이 늘어나서 만족한다는 게 직원들의 공통된 반응이었다”고 전했다. KMMG는 가동을 시작한 2009년부터 3교대로 운영하고 있다.
국내에서는 상상하기 어려운 일이다. 국내 현대차 공장은 지난 3월 근무 형태를 주야 2교대에서 주간연속 2교대로 전환했다. 현대차 노조는 근무시간이 줄어도 기존 수준의 임금을 보장해 달라고 요구했다. 결국 노사는 시간당 생산대수 등 생산성을 일부 높여 기존 수준의 생산 능력을 만회한다는 전제로 임금 유지에 합의했다. 노조는 나아가 휴일에 특근할 때 기존 밤샘특근에 적용되던 심야수당, 연장수당 등 최대 350%에 달하던 가산수당을 일부 보전할 것을 주장하며 13주간 특근을 거부했다. 이로 인해 8만 3000대(1조 7000억원)의 생산 차질이 빚어졌다.
앨라배마 공장은 자동차 업계에서 권위를 인정받는 하버리포트의 생산성 조사에서 북미 35개 자동차 공장 가운데 2010년부터 지난해까지 3년째 1위를 유지하고 있다. 자동차 한 대를 생산하는 데 걸리는 시간(HPV)이 지난해 기준 앨라배마 공장은 15.4시간으로 국내 공장(30.5시간)의 절반 수준이다. 조립라인에 필요한 표준 인원을 실제 투입된 인원으로 나눈 편성효율은 앨라배마 공장이 92.7%, 국내 공장이 53.5%였다. 편성효율이 낮을수록 적정 표준 인원보다 더 많은 근로자가 투입됐다는 뜻으로 생산성이 낮음을 의미한다.
현대·기아차는 미국에 공장을 지으면서 국내 협력업체를 동반 진출시켰다. 조지아주 애틀랜타 공항에서 앨라배마주 몽고메리시를 연결하는 85번 고속도로는 자동차 생산벨트다. 자동차 모듈을 생산하는 현대모비스를 비롯해 대한솔루션(내장재), 하이스코(강판), 한라(공조부품), 화신(섀시프레스), 만도(브레이크 등), 파워텍(변속기) 등 29개 국내 업체들이 줄지어 자리 잡고 있다.
서태영 KMMG 과장은 “자동차 품질을 확보하고 한국 부품업체들이 글로벌 경쟁력을 가질 수 있도록 동반진출을 적극 추진했다”면서 “공장과 협력업체가 가까워서 부품을 제때 공급할 수 있고, 한 업체가 조지아와 앨라배마 두 공장에 동시에 납품할 수 있어 규모의 경제에 따른 수익성 확대가 가능하다”고 설명했다.
조지아와 앨라배마 공장의 특징은 한 생산라인에서 다양한 종류의 차량을 생산할 수 있다는 점이다. 실제 생산라인에는 색깔, 종류, 선택사양이 같은 차를 찾아보기 어려웠다. 싼타페 뒤에 쏘렌토, 옵티마(국내명 K5)가 나타나는 식이다. 대중차를 양산한 뒤 판매하는 기존 방식과 차량 주문을 받은 뒤 소비자의 취향을 반영해 생산하는 주문생산방식이 섞여 있기 때문이다. 두 공장은 생산 5개월 전에 각 판매대리점의 주문을 취합해 물량을 조정하고 그에 따라 차량을 맞춤 생산하고 있다. 판매율을 끌어올리는 데 효과적이라는 평가가 나온다.
이런 생산이 가능하려면 물류 시스템이 정확해야 한다. 조지아와 앨라배마 공장은 생산라인의 정보를 종합한 전사적 자원관리 시스템을 갖추고 있다. 협력업체와도 모든 단계의 생산정보를 공유한다. 부품 생산 단계부터 재고를 최소화하고 차량의 생산 순서에 맞게 정확한 부품이 공급될 수 있도록 실어 나른다. 이러한 실시간 공정 제어 시스템 덕분에 미국 내 자동차 공장 가운데 최고 수준의 물류 경쟁력을 갖고 있다고 현대·기아차는 설명했다.
앨라배마 현대차 공장과 조지아 기아차 공장은 현재 3교대 풀가동하며 생산능력을 최대치로 발휘하고 있다. 2005년 쏘나타 9만 1000대 생산으로 시작한 앨라배마 공장은 지난해 엘란트라(국내명 아반떼)와 YF쏘나타를 각각 13만 9000대와 22만 2000대 생산했다. 조지아 공장은 2009년 1만 5000대 생산에서 지난해 옵티마, 쏘렌토, 싼타페 등을 35만 8000대 생산했다. 추가 생산 여력이 사실상 없는 상황이다.
이 때문에 일각에서는 현대·기아차가 미국에 공장을 증설할 것이라는 예상을 내놓고 있다. 노조 파업으로 국내 생산이 자주 차질을 빚으면서 공급량 부족으로 미국 내 판매가 주춤한 것도 원인이다. 지난 8월에는 네이선 딜 조지아 주지사가 정몽구 현대·기아차그룹 회장을 찾아와 추가 증설을 제안한 것으로 알려졌다.
하지만 현대·기아차 측은 신중한 반응이다. 미국에서 만난 현대·기아차 관계자는 “공장 하나 짓는 데 1조원 이상의 투자가 필요한 만큼 쉽게 결정할 수 있는 문제가 아니다”라며 “미국 시장에서 최소 30만대 이상 추가로 판매할 수 있다면 제3공장을 지을 수도 있지만 앞으로의 시장 전망에 신중할 필요가 있다”고 말했다.
웨스트포인트·몽고메리 오달란 기자
dallan@seoul.co.kr
2013-10-14 5면
Copyright ⓒ 서울신문 All rights reserved. 무단 전재-재배포, AI 학습 및 활용 금지